>never use a claw hammer for forming on an anvil...
Claw hammers, particularly low cost ones, tend to be very very hard,
Most modern claw hammers I have worked, and most screwdriver shanks and punches and prybars too, are air hardening steel. It became common a generation ago.
Now about everything you see in these tools is air hardening steel.
This makes altering them really nice! You can heat up to bright cherry and bend or manipulate them any way you like. Then just leave to cool naturally in open air. They will return to the same state you found them in, except now they will reach around the corner or whatever you altered it to do. Oh, they arc weld a treat too.
As long as you don't quench the steel when its hot, you are totally fine.
If you do quench when they are hot, they turn into unannealed glass.
One touch and they shatter.
I was adding a striking face to some cheap Chinese prybars. First 2 times I tried, I quenched the steel after welding. They snapped at the first light swat.
Only took me 2 times to figure it out though (doh :)
I've been using these bars for several years now. I am surprised they don't put striking faces on all of them! Every one of these bars I see have busted crappy handles in a short time. 3/8" mild steel plate works a treat.
To make them, you first pry the handle off and drill it the rest of the way though.
File it out square to match the shank. (Doesn't have to be perfect the handle will give some. )
Then drive the handle way down the shank, away from the heat that is to come.
Cut and weld your striking faces (let air cool) and then drive the handles back up against your new face.
A tiny quick tack bead just below the handle will keep it ever slipping back down the shank. And if you are fast it won't even heat up enough to melt your handle.
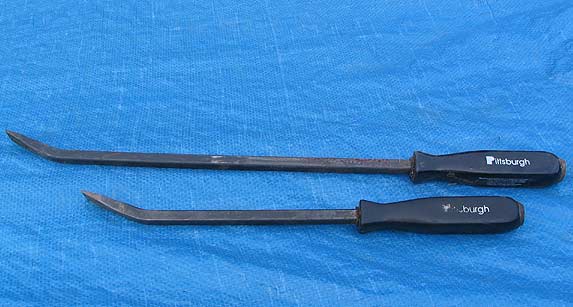
yours Scott