Yeah, Little Giant made their machines awful low! I have all of mine setting on the floor but I always think about raising them up to be more user friendly. One thing to watch is that sometimes putting the machine up on four by fours causes the machine to wobble. I always figured that any energy used wobbling was energy the machine did not put into hammering the metal! On your machine, all the movement will be down low and in line with the long axis of the machine so I don't think it will be much of a problem! I don't know how much I know but I don't mind sharing what I do know!!
Hope this helps, Bill D
Well, I was planning to build a bed of five 4x4x60's, with 1/2" all-thread running through them all to bind them together every foot. Then bolt the machine down to the bed. I can't imagine how this might cause wobbling, especially with the low center of gravity on this machine, but I'll keep an eye out for it!
Well, I shimmed out the hammer plates today, I'm treating this machine as sort of a time capsule :P The plates angled inwards ever so slightly towards the front, so the shaft wouldn't fit between them. I just made a little spacer out of 1/2" iron pipe and slipped it in there with a bolt through it, seems to do the trick. Everyone thought i was nuts when I grabbed the jars, and jars of old bolts out of my grandfather's basement when we were clearing out the house, but because of that I'm pretty well stocked for this machine! :D
I took appart the pitman arm assembly, cleaning out all the pivot points, and ground off that bubblegum. The steel underneath it looks just fine, so I'm not going to fiddle with it. I think I AM going to just replace all of these pivots with some grade 8 bolts. Yeah, it will clash with the rest of the machine, but unlike most of the other bolts, these ones are going to take a beating.
The only problem I'm milling over in my head, is the top pivot where both pitman arms come together... The original part appeared to have a central shoulder, with threads on both sides rather than being a bolt, and this central area was larger than the outside edges, presumably so the shoulders would hold the plates apart, but there's a sleeve that goes outside of THAT that is the exact same length as the shoulders, meaning that the sleeve would keep the parts spaced as well...
So, I've got a few options, I can make a new part like the original. I've got some 7/8" round stock, I can just carefully grind it into shape and thread both ends. I can get a grade 8 bolt the size of the center piece, and have to go buy a $20 drill bit so I can make the holes in the side plates big enough to accept it. Or I can find a grade 8 bolt the size of the threaded ends, and find/make a bushing... I think I like the last idea best, but I haven't decided just yet...
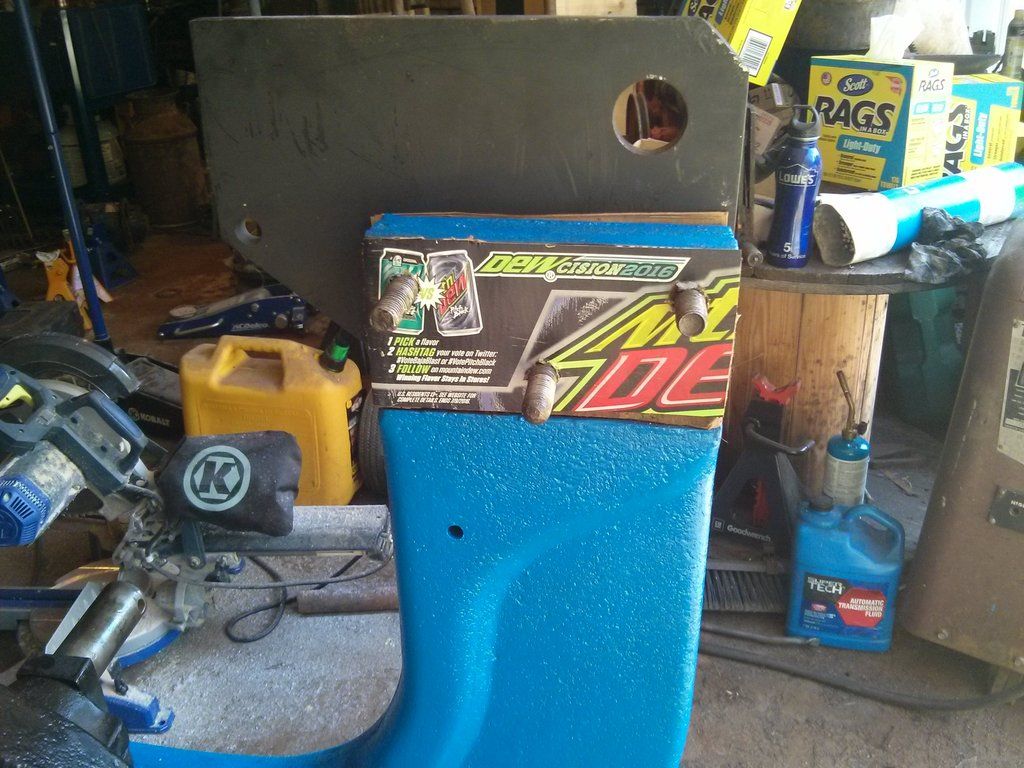
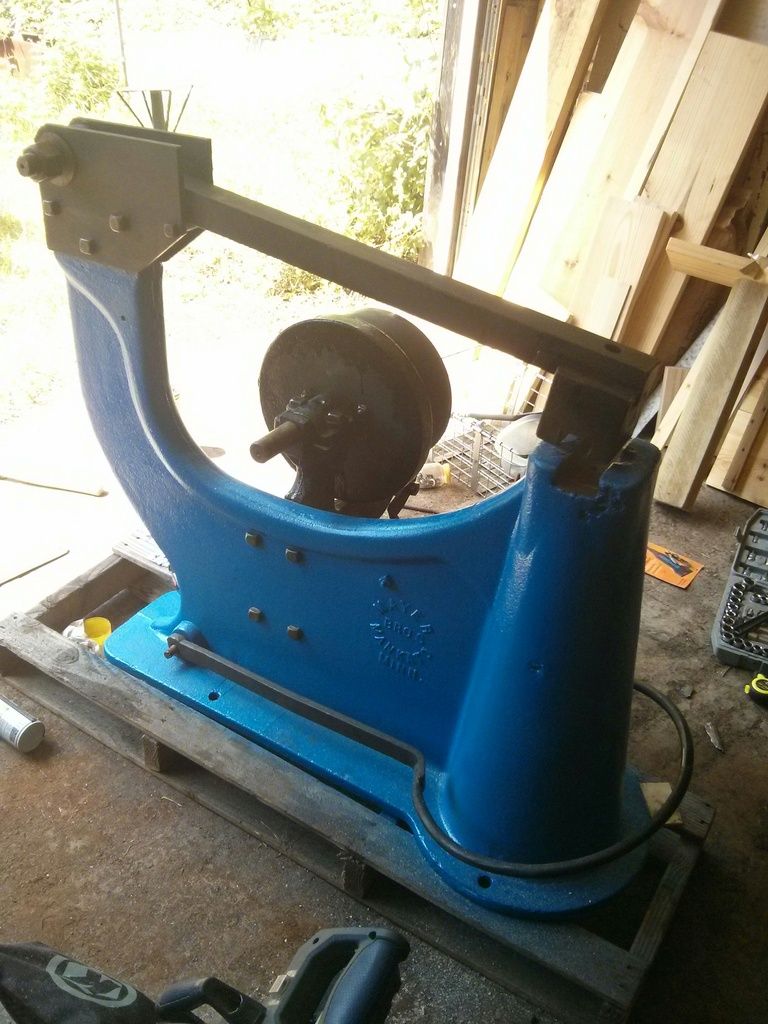
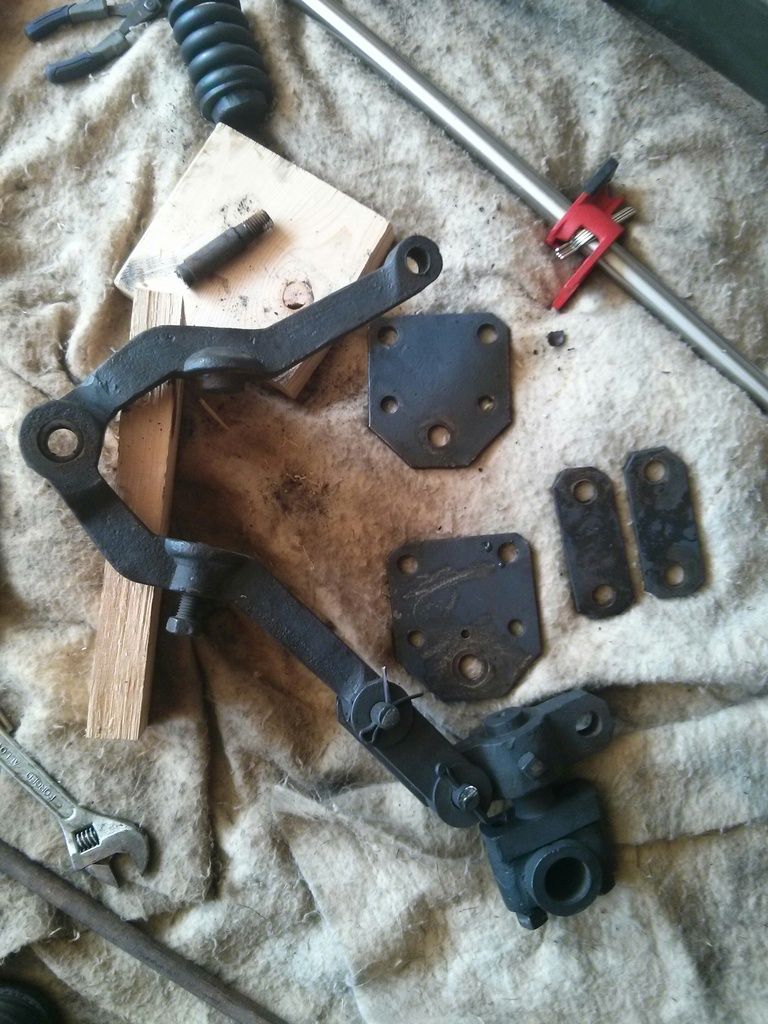