You don't really make your own touch.
You can try and you can make some stuff, but after you get tired of crude stamps, order one from Joe.
Here are two that I made. A big iron bar and a 1/4" bolt. These work well on the end grain of wood or hot metal.
Here is my touchmark my friend Peter made me. Its my little canary with my initials.
You need to be a world class jeweler to pull this off though.
Eventually will find out that restrictions abound in homemade touch marks. If you want one that is crisp and reliable, see Joe Evers at Everstamp. He is third generation at making touchmarks. You aren't going to get here by yourself.
Marks wood or metal, hot or cold, any size and design you want to order.
Just consider what you really want for a long time before you place the order.
yours Scott
http://www.henryaevers.com/
Well, thanks for the advice :3 But the people who make them professionally had to start SOMEWHERE, and I'm never gonna be great if I don't try to do things above my level. I'd prefer to make everything I need, not for frugality, but for a sense of integrity... Besides, I'm more or less just setting out. So, it doesn't have to be perfect. I won't be making perfect things for a while :3
After trying it a bit longer trying to cut a negative to stamp a piece of hot metal in to have a positive, I realized it just was never gonna work the way I want it to :P I came out with some really nice negatives, but I just couldn't get them deep enough to transfer without destroying them. So, changed tactics today and just tried to make a positive. Got pretty close, actually :D
(it looks a lot worse in the picture than it does IRL)
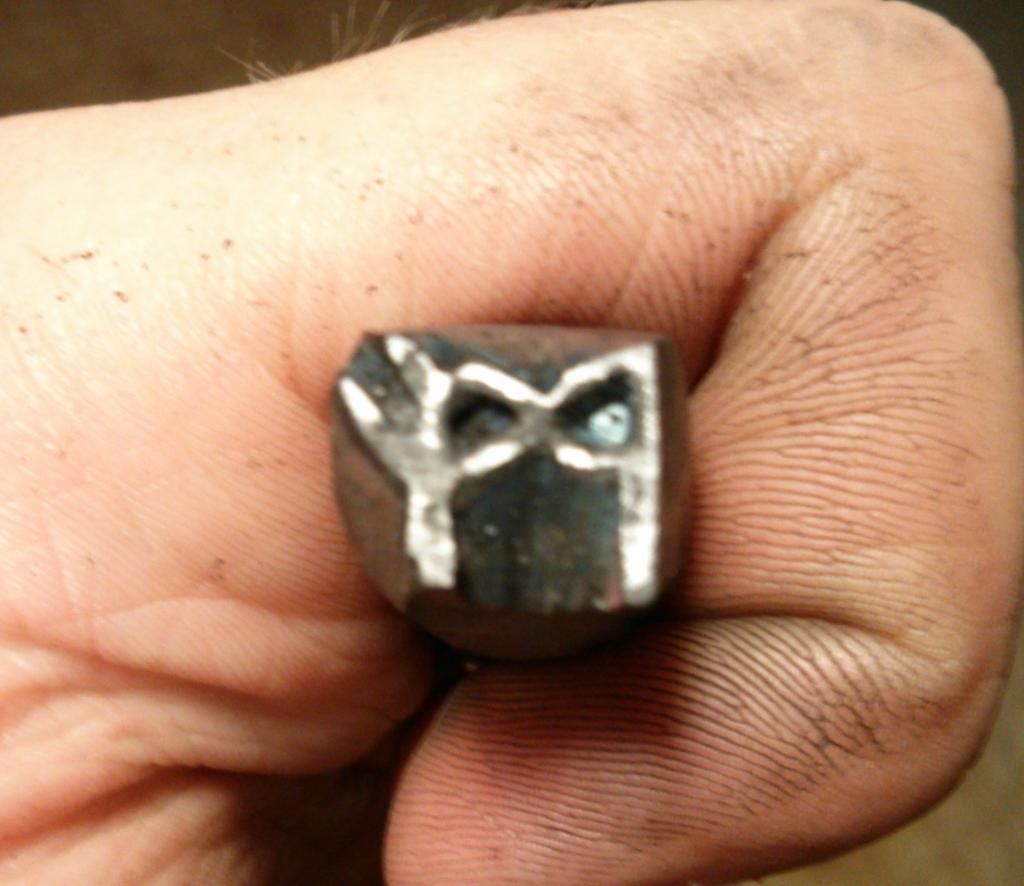
And, here's what it looked like when I heated it up and tested it on my scaling brush :P
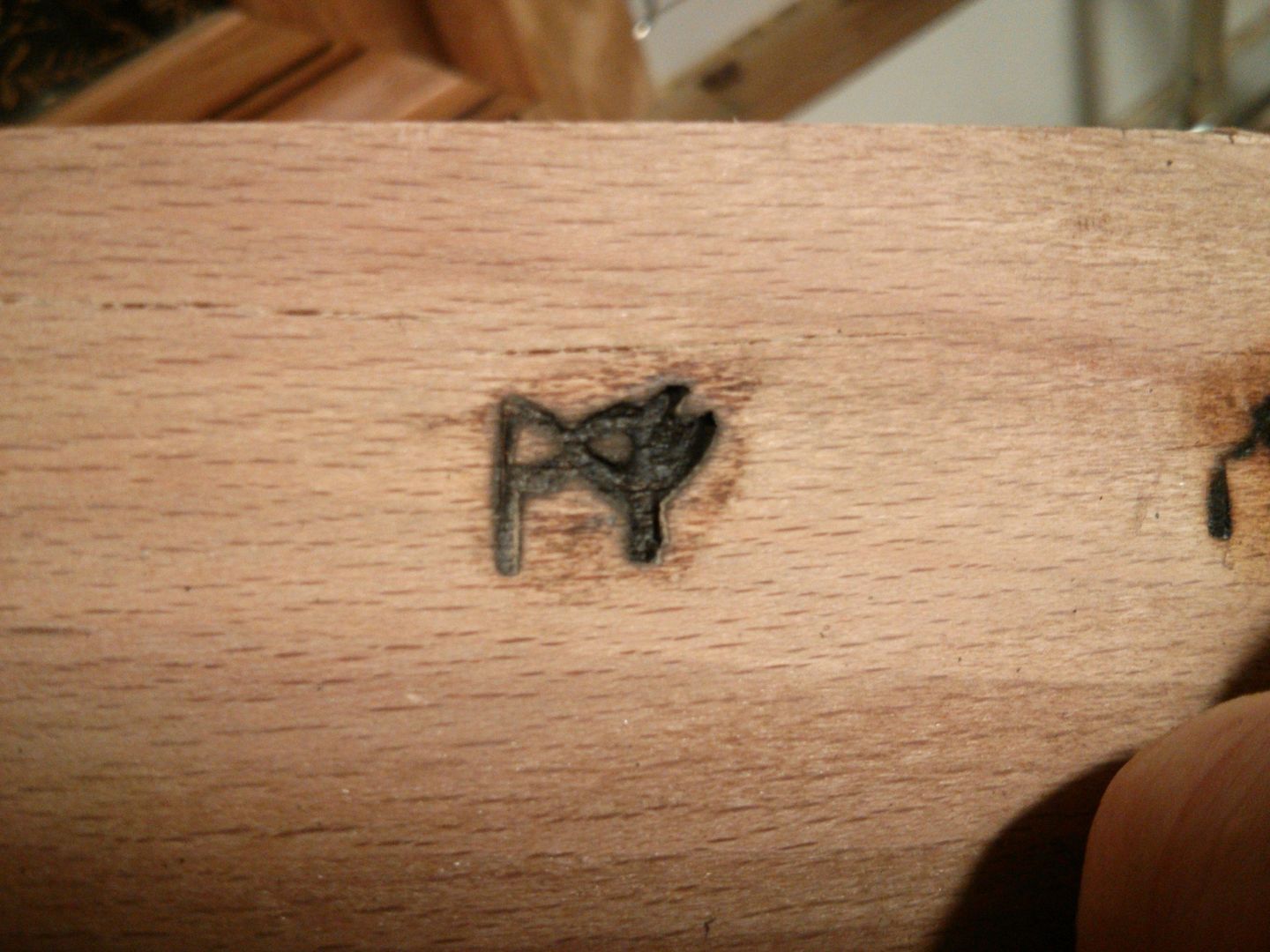
And, it should look like my logo on my business cards:
(Redacted for internet at large, not because I'm scared of you guys :P Also, while my etsy account is registered, I haven't actually started putting anything on it yet XD Included a copy of the back side too, in case anyone was wondering about the name.)
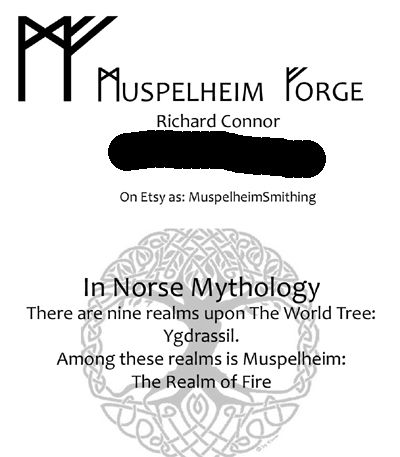
I realized before half way that the two arms on the 'F' weren't going to fit with the material I had on there, but I just kept going with it as an exercise to learn a bit. I did indeed use the suggestion offered by Lazyassforge (thanks!) Of stamping in the triangles, worked quite brilliantly. I used an angle grinder to remove the bulk of the metal around the stamp, then I used hand files to get it down to where it is. First time I've dug out my hand files, actually :x Really pleased with how well they work, no wonder they haven't completely been replaced with power tools!
When you get your touchmark, don't forget to show us some of your work!! We love pictures.
Hehe, sure thing!
My pictures just don't turn out right... I haven't set up a good well lit area for this kind of thing yet... (So many things on the to-do list!) a lot of my stuff looks worse in picture form to me than it does in hand... but, is what it is...
My most recent project, was my very first knife. Styled after a Viking knife, this is forged and tempered out of a car coil spring. Also, incidentally, my first sheath, made out of a saddle bag for a motorcycle. Ran a few rivets I made out of ground wire from some 12-2 to help protect the thread. Blade doesn't seem to get close to it, but I'd rather be safe than sorry, and it looks nice.
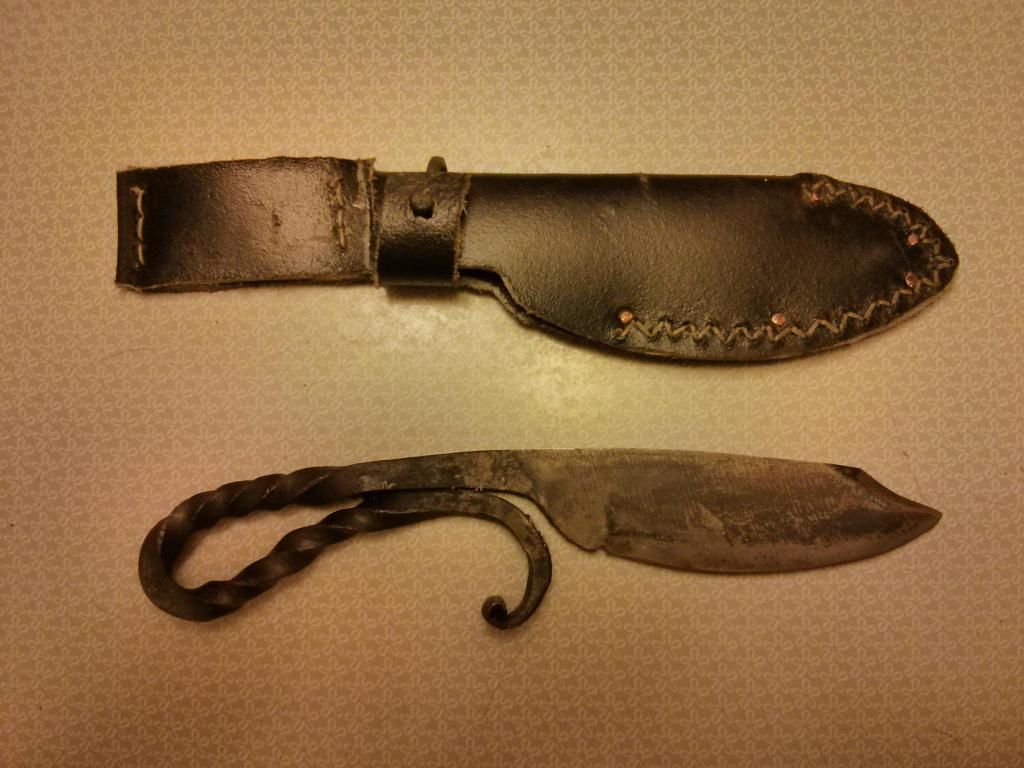
I was originally going to just put a snap on it, but I occasionally go to historical reenactments, of periods when snaps did not exist, so I invented my own little quick close system, forging out a little piece that makes it pop open with the flick of a thumb, but still secures the knife very well during normal wearing. It fit so well, and looked so pretty I didn't want to sew it on :P But, with the knife out of the sheath, it became possible for it to slip off, didn't want to lose it, so I sewed it on:
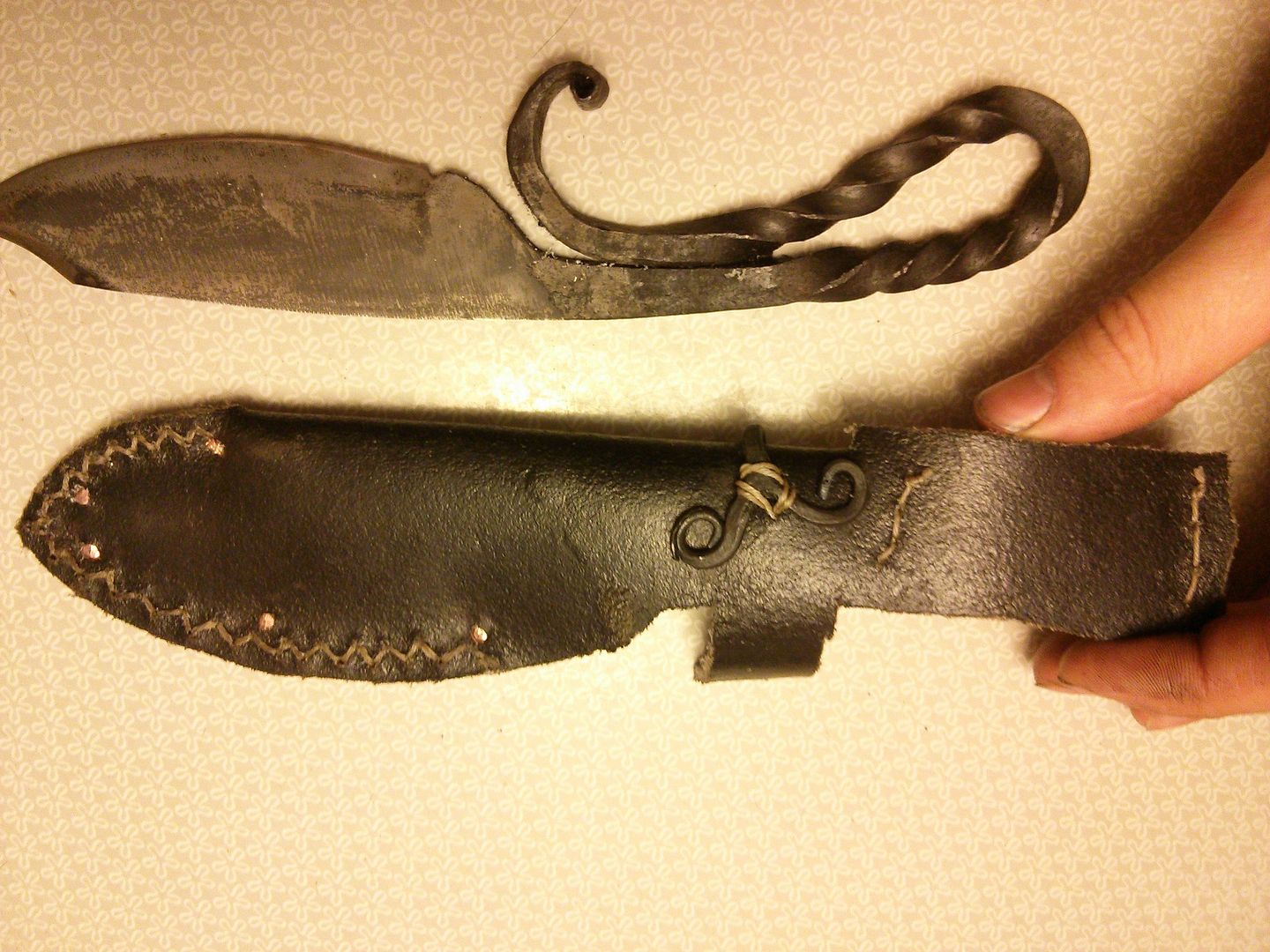
My mother does some historical reenactment as a seamstress, she asked me to make her some closures for her cloaks, so I made these two clasps made of 1/4" square stock:
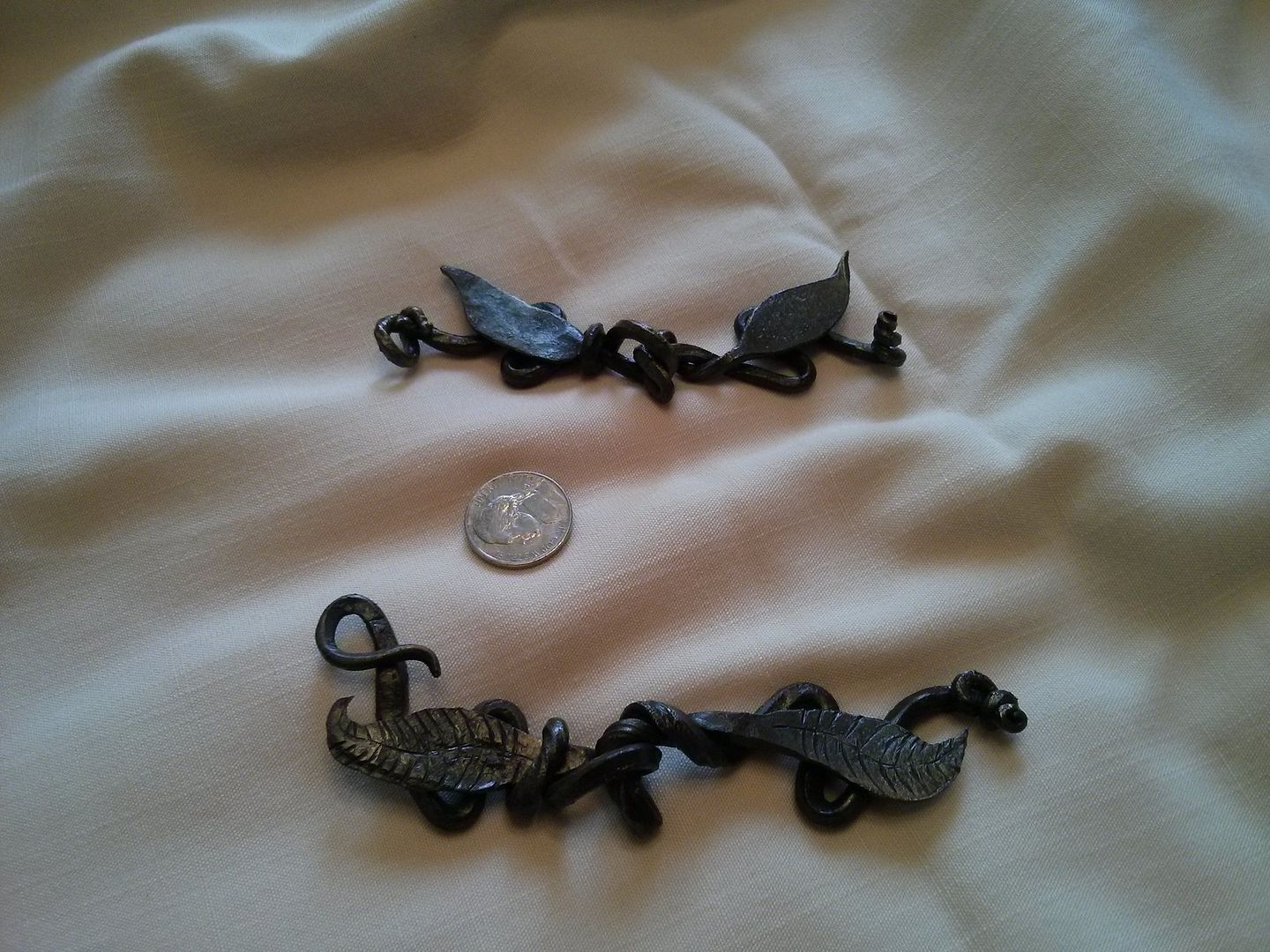
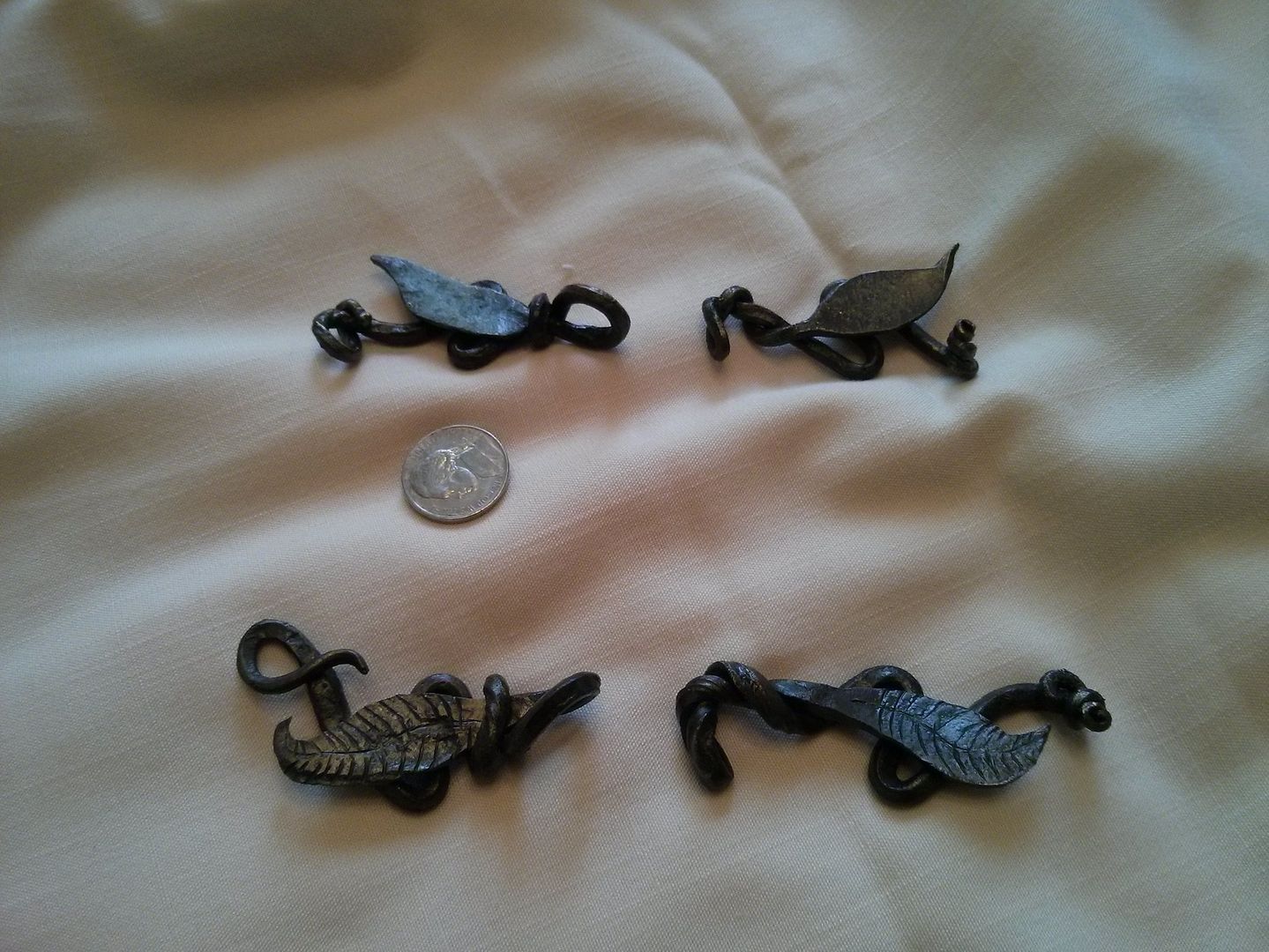
She was making a cloak for my sister, and I thought I would be clever and surprise her. She likes cats, so instead of leafy vines, I was gonna try to make two cats with inter-locking tails out of 3/8" square stock, but, at about this point:
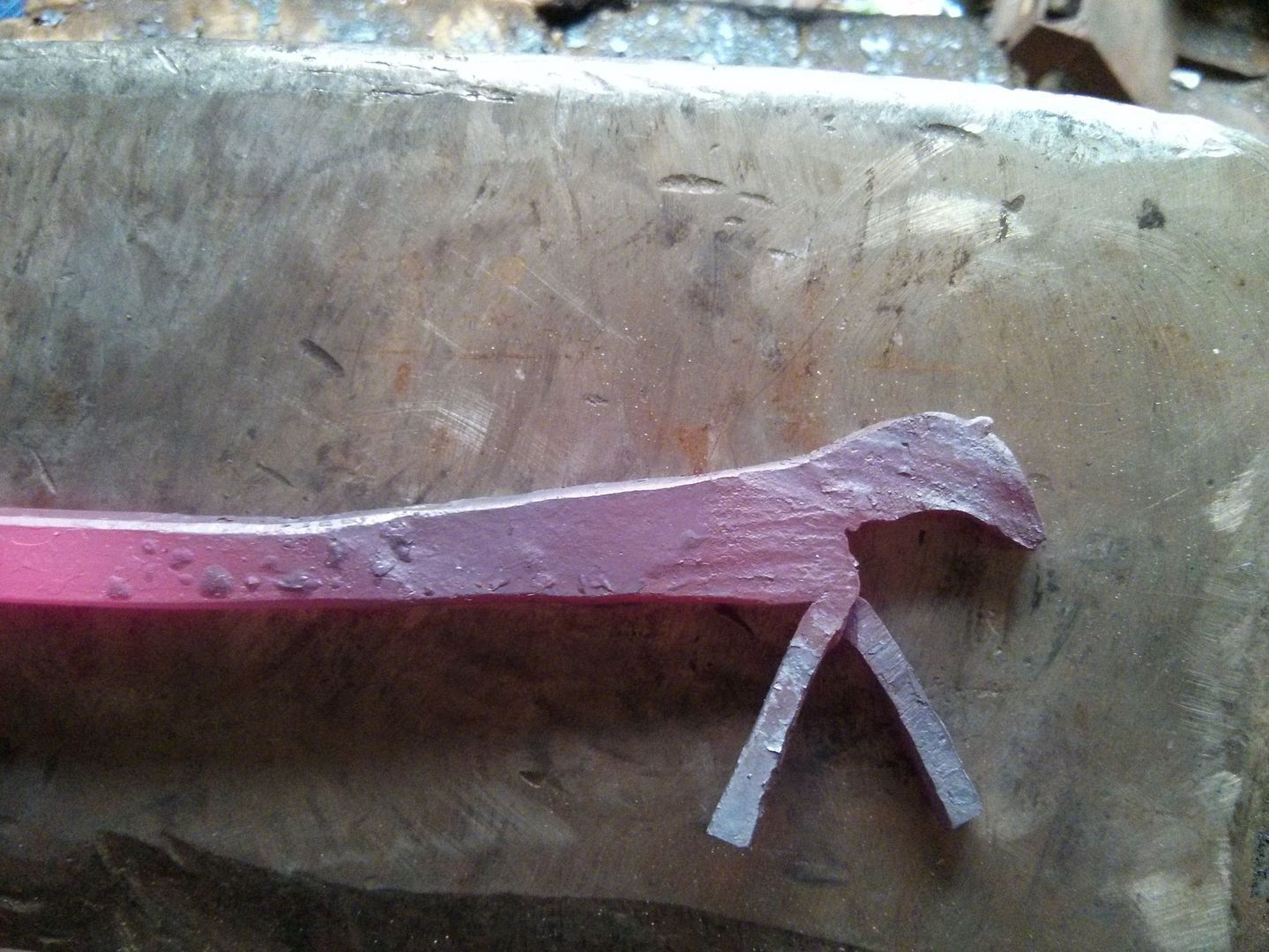
It very clearly looked like a horse, not a cat... so I went with it! It's actually my favorite piece :P Not my BEST piece, but my favorite one. It's currently living it's life as a refrigerator magnet on my fridge.
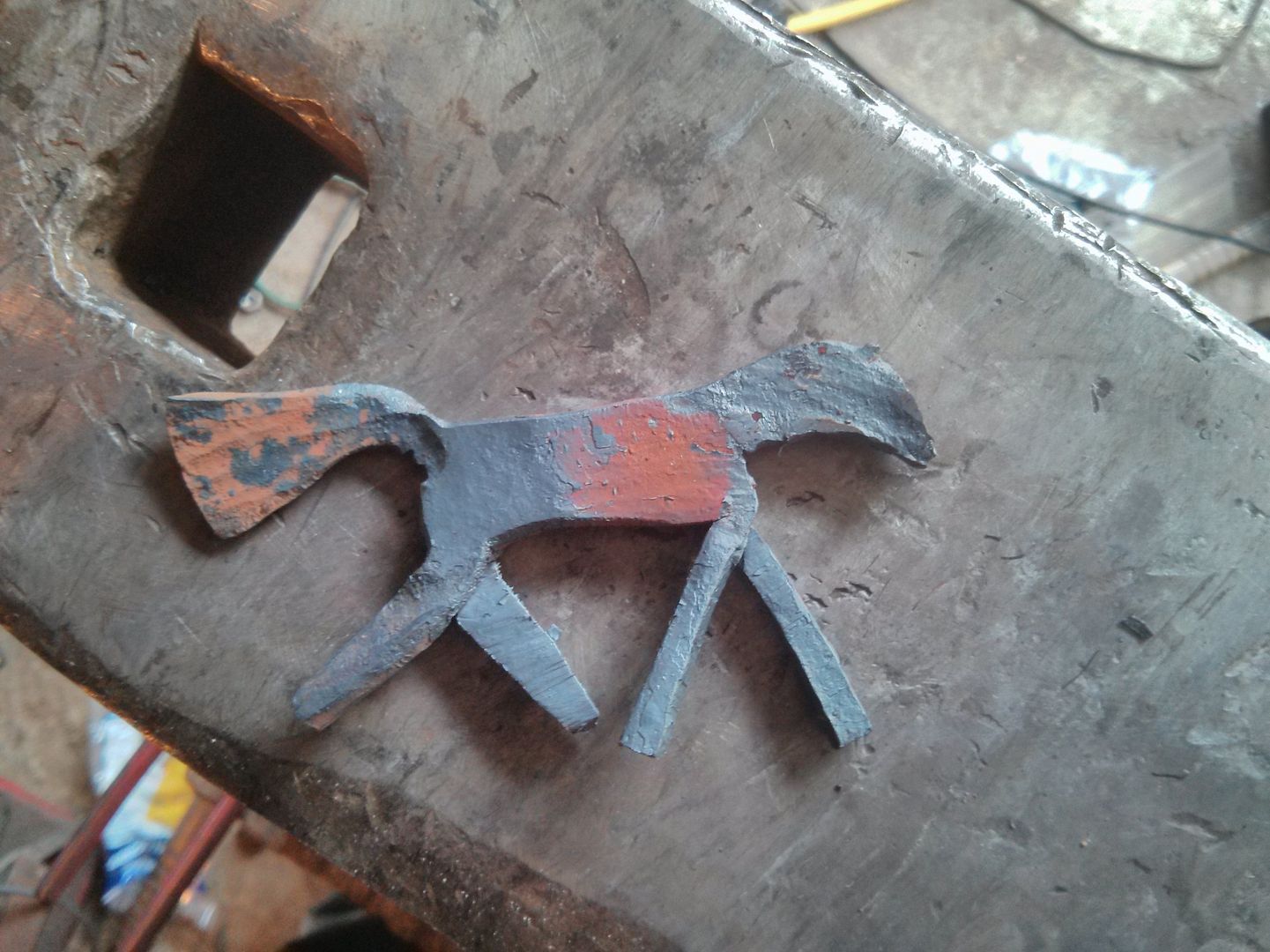
My first commissioned piece, was this door knocker. Made from 1/2" square stock. Picture really sucks... but you grab the little acorn and it's on an arm that knocks against the leaf, which is supported by a nice chunk of steel that transfers sound well:
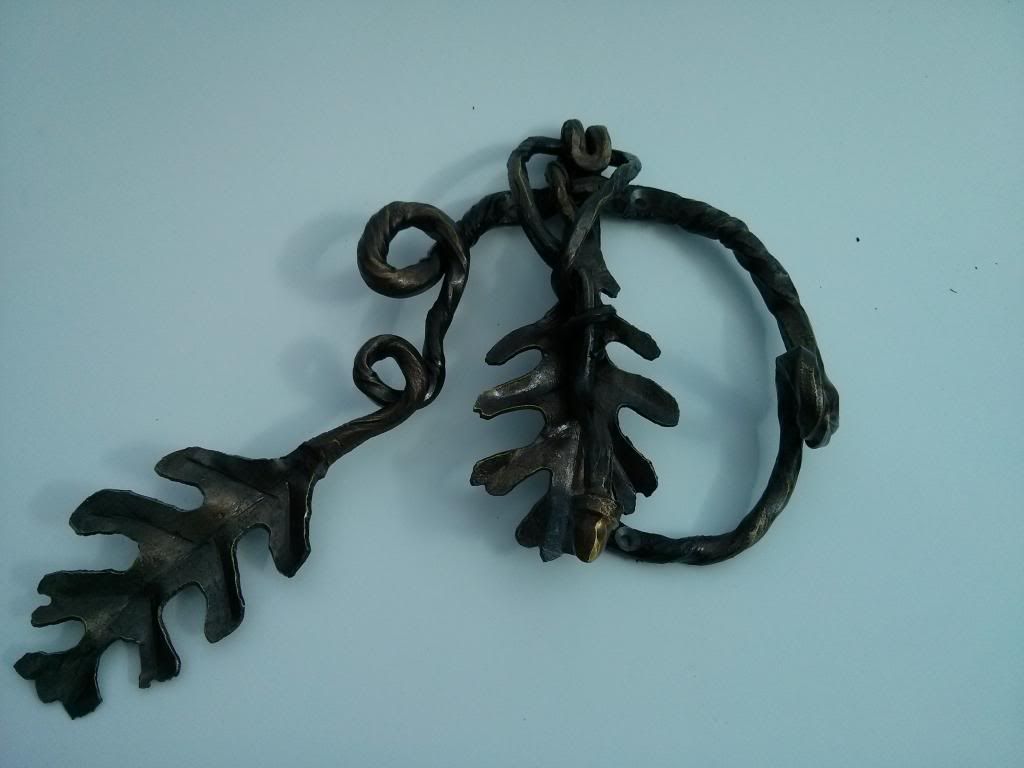
And, then these were just plane some of my first projects, towel bars, TP holders made of 3/8" round stock, and some 1/4" sq. stock robe hooks.
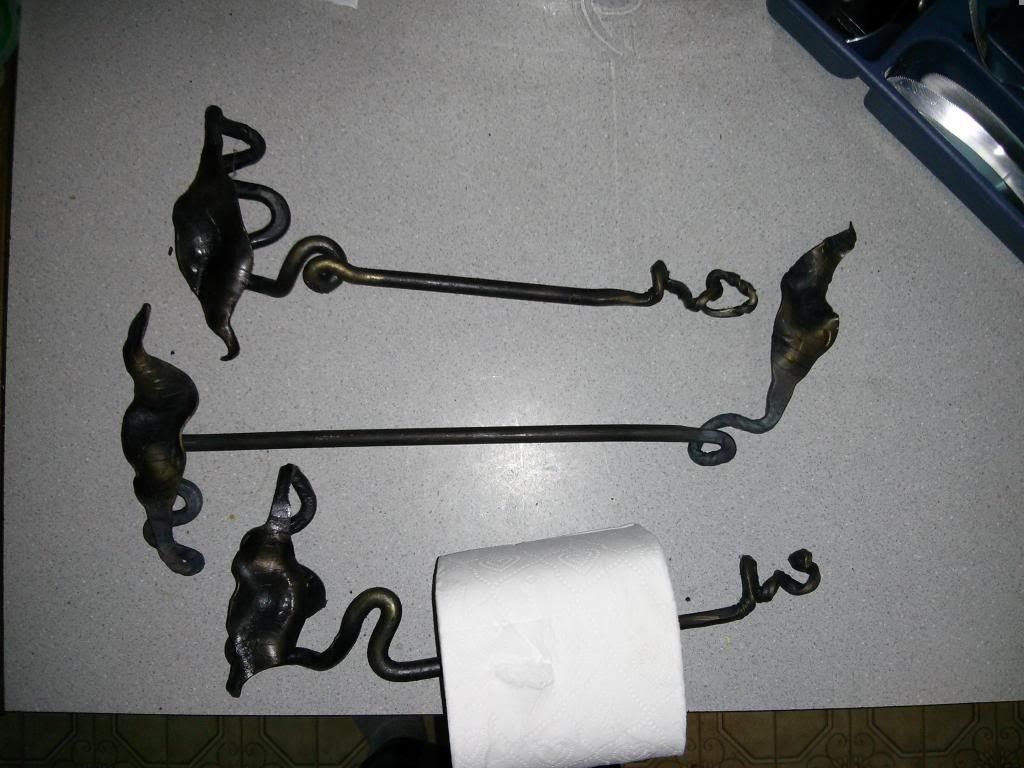
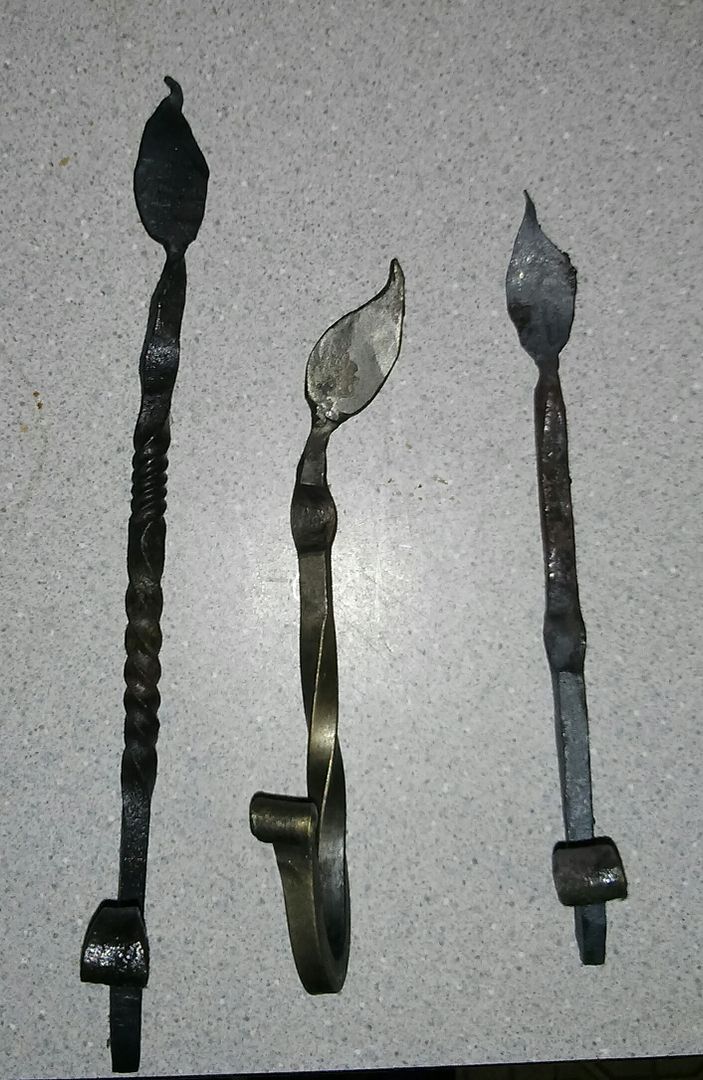